3 min read
The Production Process of PVC-O: Creating a Bi-Oriented Pipe with Optimal Strength
Joe Venegas
Jun 20, 2024 8:37:03 AM
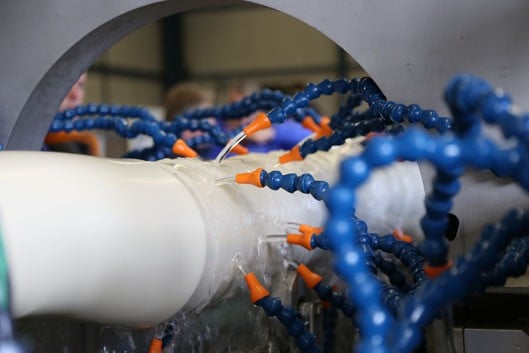
Bi-Oriented Polyvinyl Chloride PVC-O is a leap ahead in the PVC industry, showcasing properties that set it apart; including superior strength, robustness, and lightweight. The meticulous execution of a highly precise pvc pipe manufacturing process and pipe manufacturing process is imperative for materializing these attributes. This article aims to dissect this pipe production machine driven production process, laying bare details to aid a better understanding of the methods and tactics required for the manufacture of a high-quality bi-oriented pipe.
The Essentials of PVC-O Production
Setting Ground with U-PVC Pressure Pipe
From a birds-eye view, a PVC-O entity is born from the manufacturing of an Unplasticized Polyvinyl Chloride (U-PVC) pressure pipe. U-PVC pipe is made by dry-blending PVC resin with additives and pigments, taking the blended material into a twin-screw extruder, and subsequently undertaking melt processing to form a homogenous and incessant pipe. This is a crucial step in the pvc pipe making process using a pvc pipe manufacturing machine.
Pertinence of Temperature Control and Cooling Phase
The process of producing PVC-O products significantly rests upon exact temperature control. A stable heating phase to a temperature of 85-100 degrees Celsius (185-212 degrees Fahrenheit) is crucial to soften the U-PVC material, whereas a rapid cooling phase is essential to solidify the newly formed molecular alignment. To sustain strict conditions throughout the process, the employment of dedicated cooling systems and temperature sensors is indispensable in the overall pipe manufacturing process.
Diameter Expansion of the Pipe
At the targeted temperature, the pipe's diameter is expanded using an internal pressure or force. The required diameter stretching ratio depends on the required material strength (in ISO standards named as MRS value) and the stretching temperature. Generally, the diameter stretching ratio is between 1.6 and 2.1. Higher stretching ratios result in higher MRS values. Maintaining the expanded diameter, the pipe is subsequently cooled, freezing it into its new shape. The precise temperature control in this stage is vital to achieve the desired molecular orientation, hence improved mechanical properties. This phase is a key part of the pvc pipe making process utilizing advanced pipe production machines.
Orientation in PVC-O Pipe Production
The Mono Axial Stretched Pipe
By examining the molecular changes during the expansion process, we can understand the significance of orientation. If a small ring is taken from the initial pipe and stretched at the proper temperature, its weight remains the same before and after expansion. However, this process results in a reduction of both the pipe's wall thickness and its length, creating a mono-axially stretched ring. Such a pipe is not an accurate representation of PVC-O, which is typically bi-oriented.
Achieving Bi-Orientation in PVC-O Pipes
To create a bi-oriented PVC-O pipe, the length of the preform must be maintained during the stretching process, while simultaneously increasing the diameter. This approach leads to an even greater reduction in wall thickness. Consequently, the orientation occurs not only in the pipe's circumference but also in the length direction.
The Rollepaal Inline Process
Rollepaal's production of PVC-O pipes is achieved through an advanced inline extrusion process, developed specifically for achieving bi-orientation. Our technique guarantees constant wall thickness, optimal molecular alignment, and outstanding product performance. Rollepaal's industry-leading techniques build upon decades of expertise in pvc extrusions and orientation engineering, all integrated within a modern pvc pipe manufacturing machine environment.
The Role of Length Stretch in PVC-O Production
Bi-Oriented Pipes with Length Stretch
The Rollepaal process and other inline processes enable manufacturers to also increase the physical length of the preform during the stretching stage. In this case, the final result is a bi-oriented pipe combined with a length stretch. The strength and other properties of the pipe remain unaffected by the addition of the length stretch.
Integrated Sockets and Optimal Strength
Practical experience in sustained pressure testing has shown that creating sockets as an integral part of the pipe results in higher socket strength when the pipe includes a length stretch. A length stretch of approximately 20 percent will yield optimal strength for the integrated sockets.
Conclusion
Temperature control and orientation are crucial elements in PVC-O pipe production, ensuring optimal mechanical properties and performance. By applying precise temperature management and techniques such as bi-orientation and length stretch, manufacturers can produce high-quality PVC-O products. Rollepaal's dedication to professionalism and detail guarantees reliable and efficient solutions tailored to meet the industry's highest standards.
Explore the Innovative World of PVC-O: Production Processes, Technological Evolution, and Performance
Understand the PVC-O production techniques, technological advancements, and the superior performance attributes that set PVC-O apart in the industry. From the birth of bi-oriented pipes to the evolution of inline processes, and the innovative Rollepaal PVC-O production - our guide provides an informed and in-depth look into this remarkable material.