3 min read
The Rollepaal PVC-O Pipe Production Process: Excellence in Innovation
Joe Venegas
Jun 19, 2024 8:04:34 AM
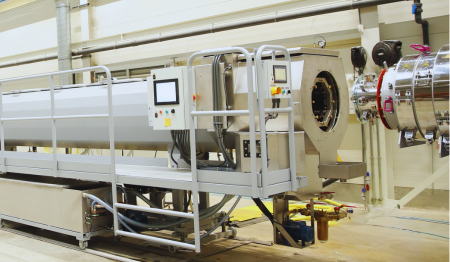
Rollepaal is renowned for its cutting-edge technology in the production of PVC-O plastic pipes. Underpinning this reputation is our proprietary air-based in-line process known as Rollepaal PVC-O. This article explains the various steps involved in the Rollepaal PVC-O plastic pipe production process, aiming to provide you with a comprehensive understanding and highlighting the features that differentiate us in the marketplace.
Step-by-step Rollepaal PVC-O Process
Rollepaal PVC-O is an intricate process encompassing several stages to ensure accuracy, uniformity, and efficiency. These stages are carried out meticulously to ensure a uniformly thick preform, optimal temperature profiles, careful expansion, precise calibration, appropriate length orientation, continuous pipe cooling, and auto-control when the line is running.
Stage 1: Creation of the Preform
The process commences with the creation of the preform. Employing a die-head featuring an Automatic Thermal Centering function, we ensure a uniform wall thickness for the preform while maintaining 100% welding line strength. The preform speed is meticulously regulated using a cooling tank and a small haul-off, resulting in a uniform preform wall thickness in this segment of the line.
Stage 2: Establishing Optimal Temperature Profile
The next stage emphasizes conditioning the pipe to establish an optimal temperature profile. This process is achieved using specific conditioning units that employ hot air. With a skin cooler, a thin, stiff layer on the outer pipe wall is established to obtain the required pipe ring stiffness to pass the haul-off.
By means of an infrared heater, the required heat is infused in the outer pipe wall just before the orientation process.
Stage 3: Expansion
The third stage involves the expansion of the pipe on our mandrel by means of compressed air, a critical phase that guarantees uniformity and continuous stretching of the pipe. Our expertise in air treatment affords us precision at this stage.
This stage of the process is protected by means of essential Rollepaal patents.
Stage 4: Pipe Calibration
In the fourth stage, the pipe undergoes calibration. Here, we use conditioned and compressed air to support the pipe interior, while cooling the pipe exterior. This process allows the pipe to solidify at the correct dimensions and ensures the optimal wall thickness distribution.
This calibration principle is also covered by essential Rollepaal patents.
Stage 5: Length Orientation
The focus of step five is to set up the required length orientation. We control the speeds of the pullers both before and after the mandrel to achieve this.
Stage 6: Pipe Cooling
In the sixth step, the pipe is cooled down straight after stretching. The wall thickness is immediately measured after cooling. Infrared heaters upstream of the mandrel optimize the wall thickness distribution around the pipe.
This is a continuous procedure, ensuring consistency throughout the pipe's length.
Stage 7: Automatic Running
Once the line starts running, it operates on automatic air control and wall thickness control. This automation ensures optimal running conditions and consistent pipe dimensions.
Rollepaal PVC-O Process – Detailed Insight
The Rollepaal PVC-O process is executed using an advanced system comprising an extruder and a die-head. A distinctive feature is the 'off-set extruder'. The off-set extruder facilitates the passage of the pulling bar through the die head and provides for internal cooling of the pipe. There's also a two-track haul off used during startup and as a backup for situations where extra force might be required.
The line layout can be adjusted to fit your factory's needs, with the pulling bar console continuously measuring the pulling force to monitor process stability. Also, we utilize several air pipelines within the pulling bar to regulate air flow and pressure during the stretching process.
To produce a thick preform, we use triple compression die head tooling, Rollepaal patented branching and automatic thermal centering at the die's exit.
Remote Data-Driven Support
The Rollepaal PVC-O line is controlled by two sets of PLC's, one in the extruder and one in the stretching unit. With more than 200 data points on set points and actual values collected every 5 seconds, we encourage customers to store this data directly in the cloud. This allows us to provide remote support, to quickly identify and address issues, as well as continuous process improvement.
Specifications and Patents
The Rollepaal PVC-O line is capable of creating MRS 31,5 up to 50, diameters 90 to 630, and pressure classes PN12,5 up to 25 in ISO. In the AWWA C909, we can handle diameters 4 inch up to 24 inch in Pressure Class 165 up to 305. Outputs can reach 1000 kg/hour, and the line speed is currently limited to 300 m/hour. Rollepaal PVC-O is also capable of producing pipe for other standards.
We currently hold multiple patents applicable to our process, protecting our innovative line worldwide.
In conclusion, our Rollepaal PVC-O process offers an innovative, efficient, and precise manufacturing process for PVC-O pipes, supported by our technical expertise, industry-leading specifications, and patented technologies. Here at Rollepaal, we're leaders in delivering excellence, turning complex processes into straightforward solutions.
Explore the Innovative World of PVC-O: Production Processes, Technological Evolution, and Performance
Understand the PVC-O production techniques, technological advancements, and the superior performance attributes that set PVC-O apart in the industry. From the birth of bi-oriented pipes to the evolution to inline processes, and the innovative Rollepaal PVC-O production - our guide provides an informed and in-depth look into this remarkable material.