Multi-Layer Technology
Up to 70% virgin material reduction
What is Multi-Layer Extrusion Technology?
Multi-Layer extrusion is a process that involves the co-extrusion of multiple polymer layers into a single pipe structure. This technique allows manufacturers to combine different materials, each imparting unique properties to the final product. Typical configurations involve a core layer made from recycled or less expensive foamed materials, encapsulated by higher-grade PVC that provides the necessary surface qualities and mechanical strength.
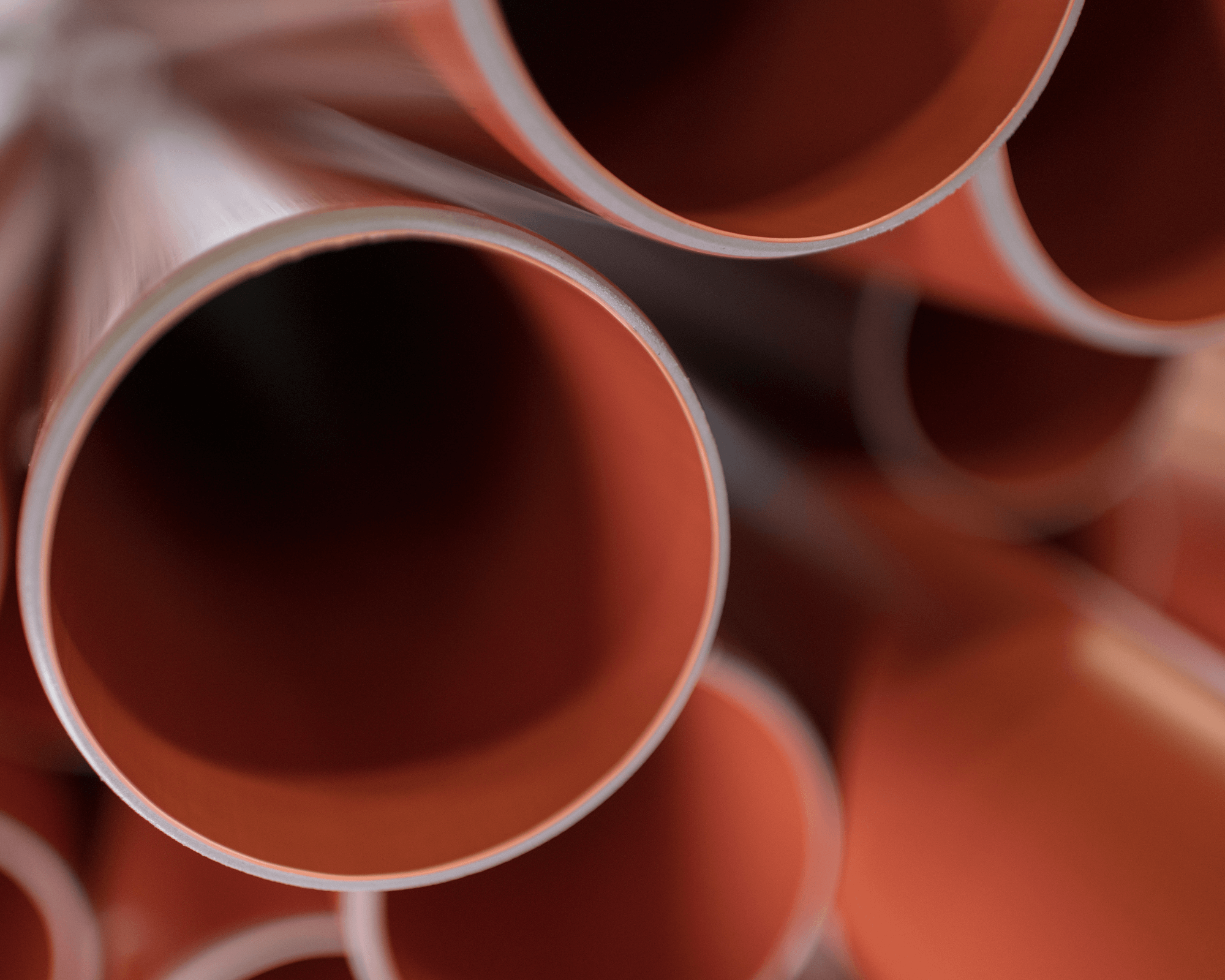
The Benefits of Multi-Layer Extrusion
1. Raw Material Savings
- Core Layer Utilization: Using recycled or lower-cost materials in the core layer can significantly reduce material costs. Only the outer layers must be made from high-grade PVC, which are more expensive.
- Enhanced Material Efficiency: The precise control of layer thicknesses minimizes waste material, leading to more efficient use of inputs.
2. Improved Product Properties
- Customization of Pipe Characteristics: The ability to tailor the properties of each layer results in a pipe that meets specific performance requirements. For instance, the outer layer can be optimized for UV resistance, while the inner layers provide structural integrity.
- Enhanced Durability: Pipes produced using Multi-Layer extrusion often exhibit better durability and longevity due to the synergistic effects of the combined materials.
Required Equipment
A series of equipment is required to ensure the production process’s quality, efficiency, and precision. Below is an overview of the key equipment used in the manufacturing of Multi-Layer pipes.
1. Extruders
Extruders are essential machines that deploy a screw mechanism to melt and shape the plastic material. In the context of Multi-Layer pipes, multiple extruders are used for different layers:
Primary Extruder: This handles the core layer, which is made from foamed materials, high-filled materials, or recycled content.
Secondary Extruder(s): Used for outer and inner layers, ensuring uniformity and structural integrity.
Read more about Twin Screw Extruders
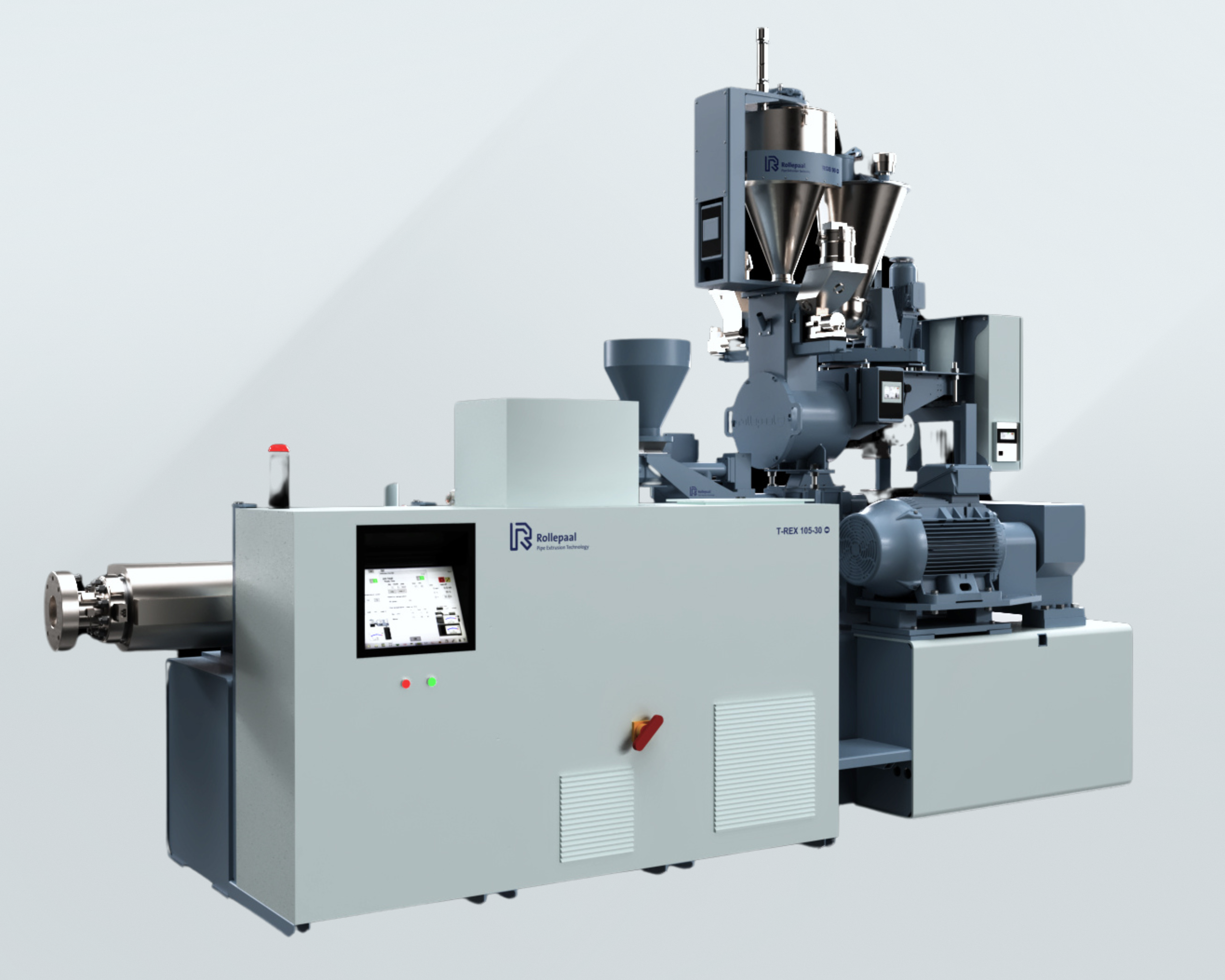
2. Gravimetric Systems
Gravimetric systems are measurement devices that regulate material feeding into extruders, ensuring consistent output and minimizing waste.
Rollepaal Gravimetric Systems optimize material flow for stable extruder output, even with bulk density fluctuations. Their automated calibration reduces overweight and ensures precise dosing. Designed for efficient mass flow, these systems enhance productivity while minimizing waste and costs.
Read more about Feeders & Gravimetrics
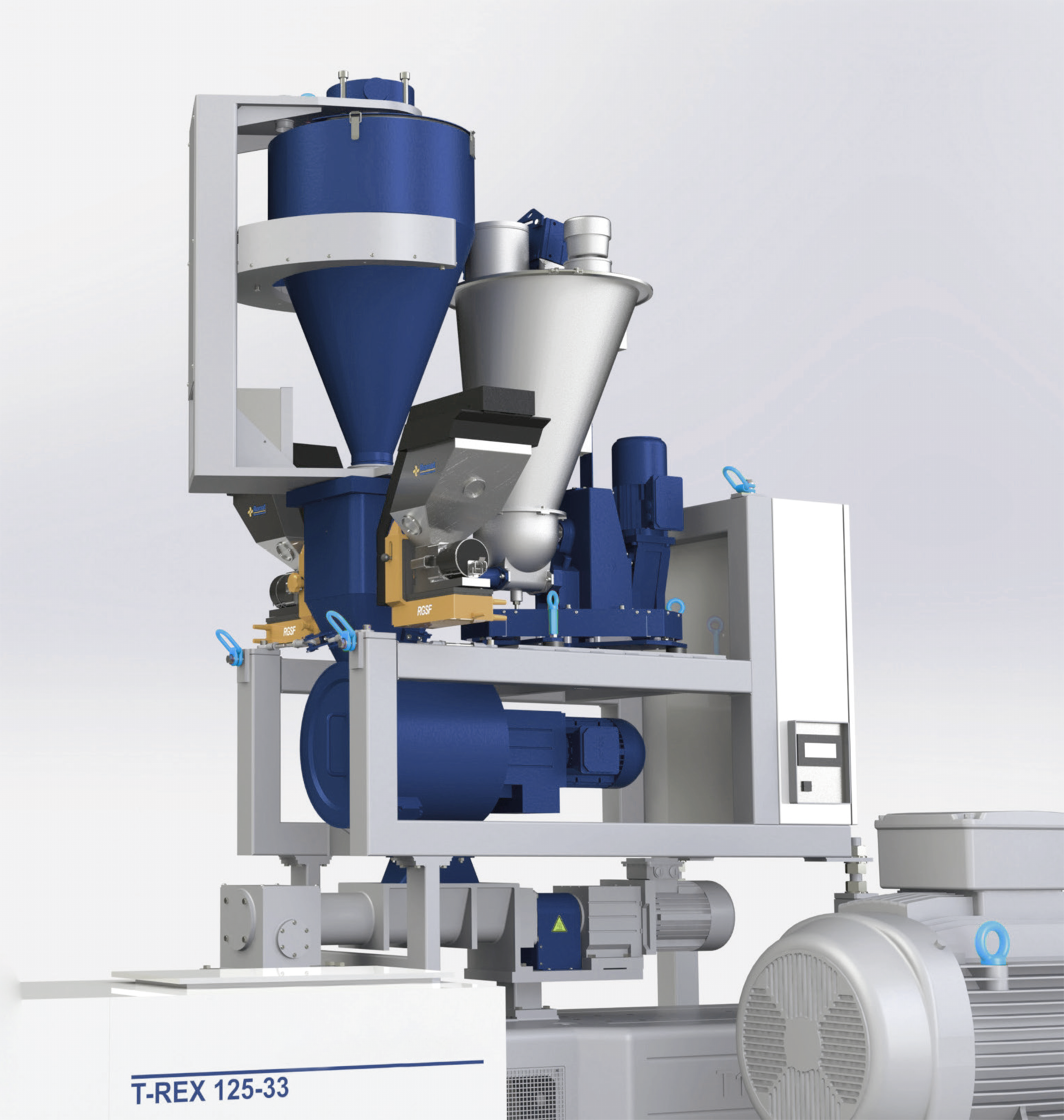
3. Multi-Layer Die Head
Multi-Layer die heads are critical in the formation of Multi-Layer pipes. These components are engineered to combine multiple melts from different extruders into a single Multi-Layer pipe. Key type is:
Offset Die Principles (Discs): Discs with even branching channels prevent leakage and ensure consistent layer distribution.
Read more about Multi-Layer Die Heads
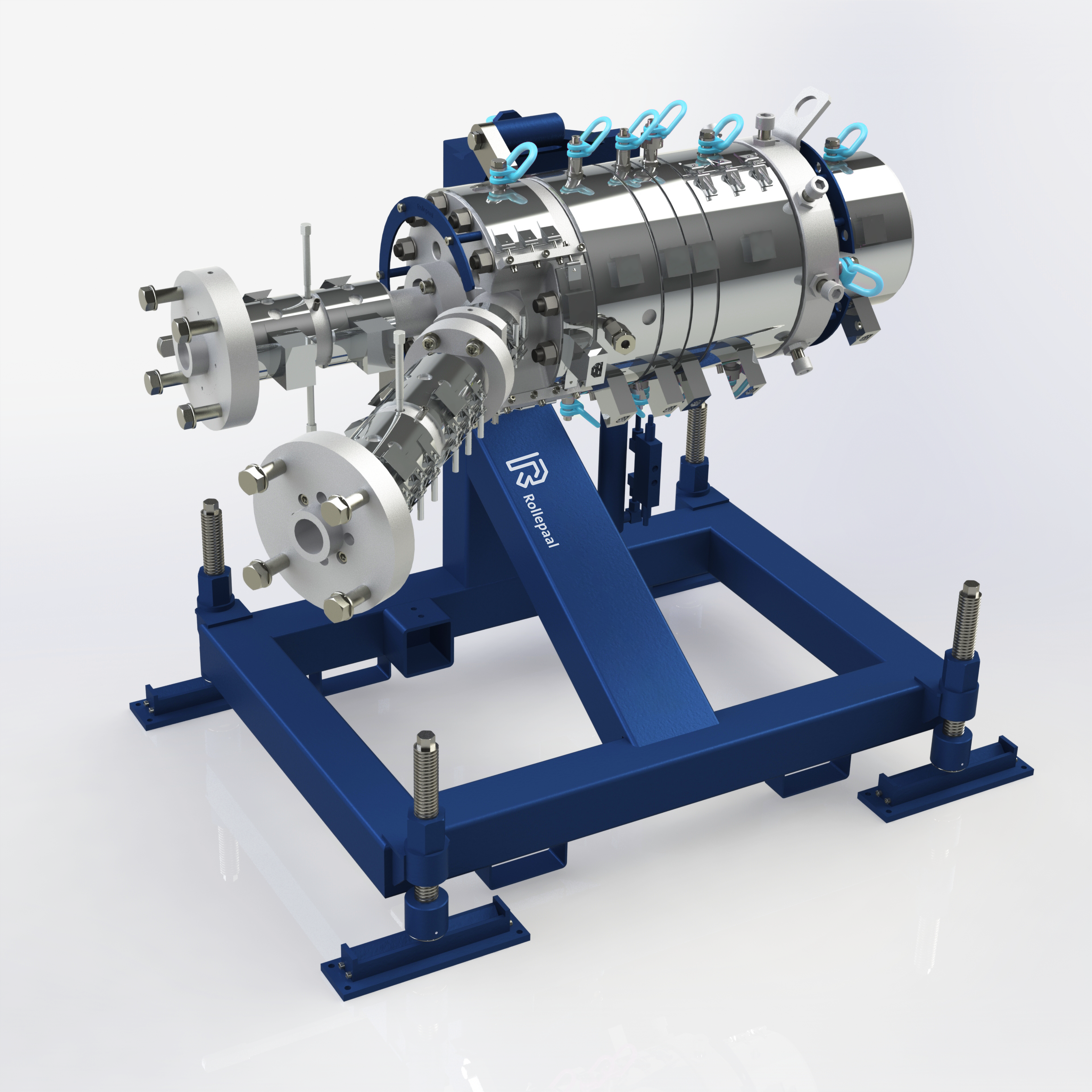
4. Cooling System
The formed pipes must be cooled rapidly to maintain their shape and structural properties. Two types of cooling units are typically used:
Vacuum Cooling: This method rapidly cools pipes after extrusion by applying a vacuum to prevent ovality of the pipe.
Spray Cooling: Positioned after the vacuum cooling section, this system sprays water under atmospheric conditions for additional cooling and optimal results.
Read more about Cooling Units
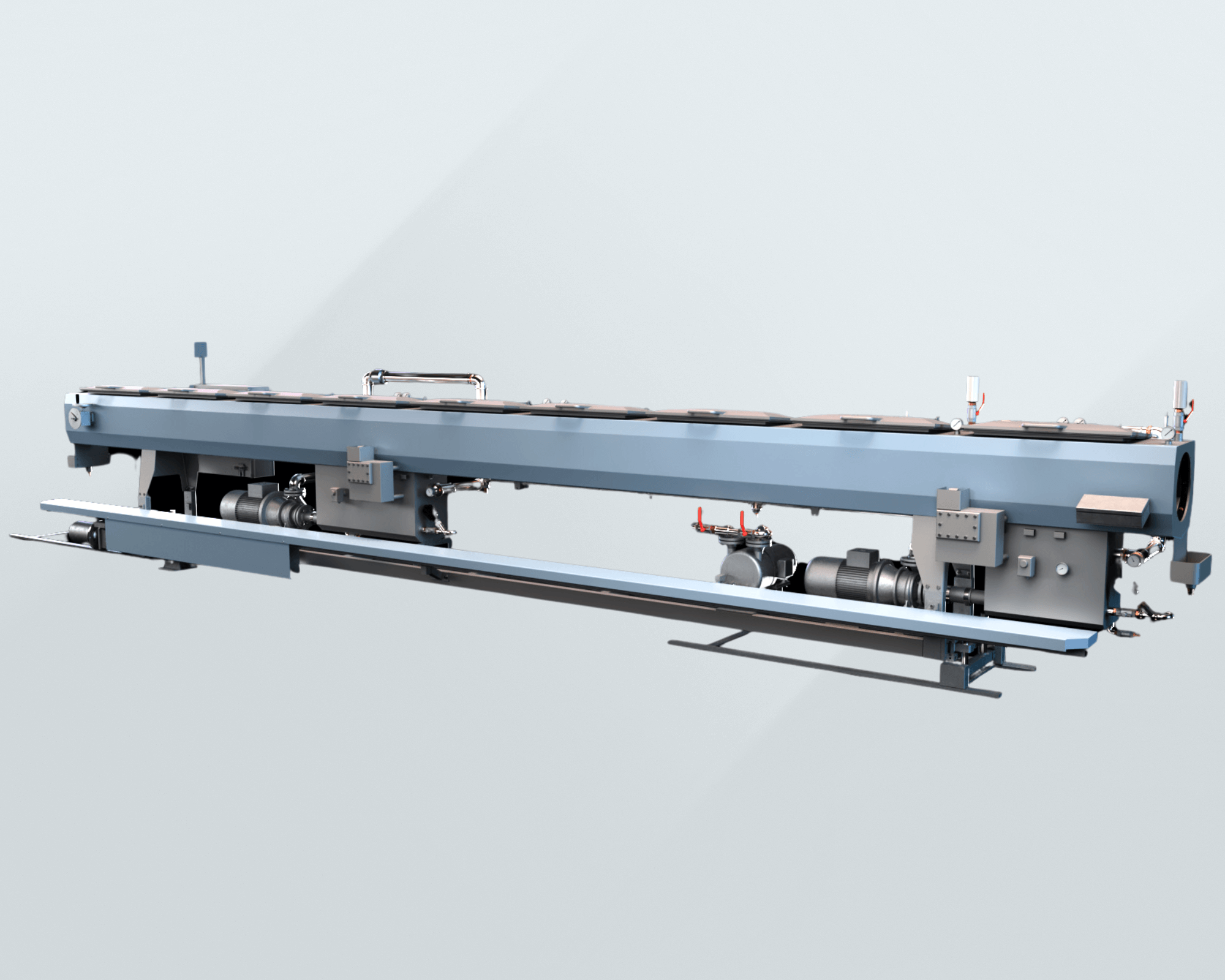
5. Haul-Off
These units are responsible for drawing the extruded pipe through the cooling system at a consistent speed, ensuring uniform pipe dimensions and preventing deformation.
To protect the pipe surface, our haul-offs feature rubber blocks that cushion against direct contact, reducing the risk of scratches, dents, or imperfections. This ensures high-quality production that meets customer expectations.
Read more about Haul-Offs
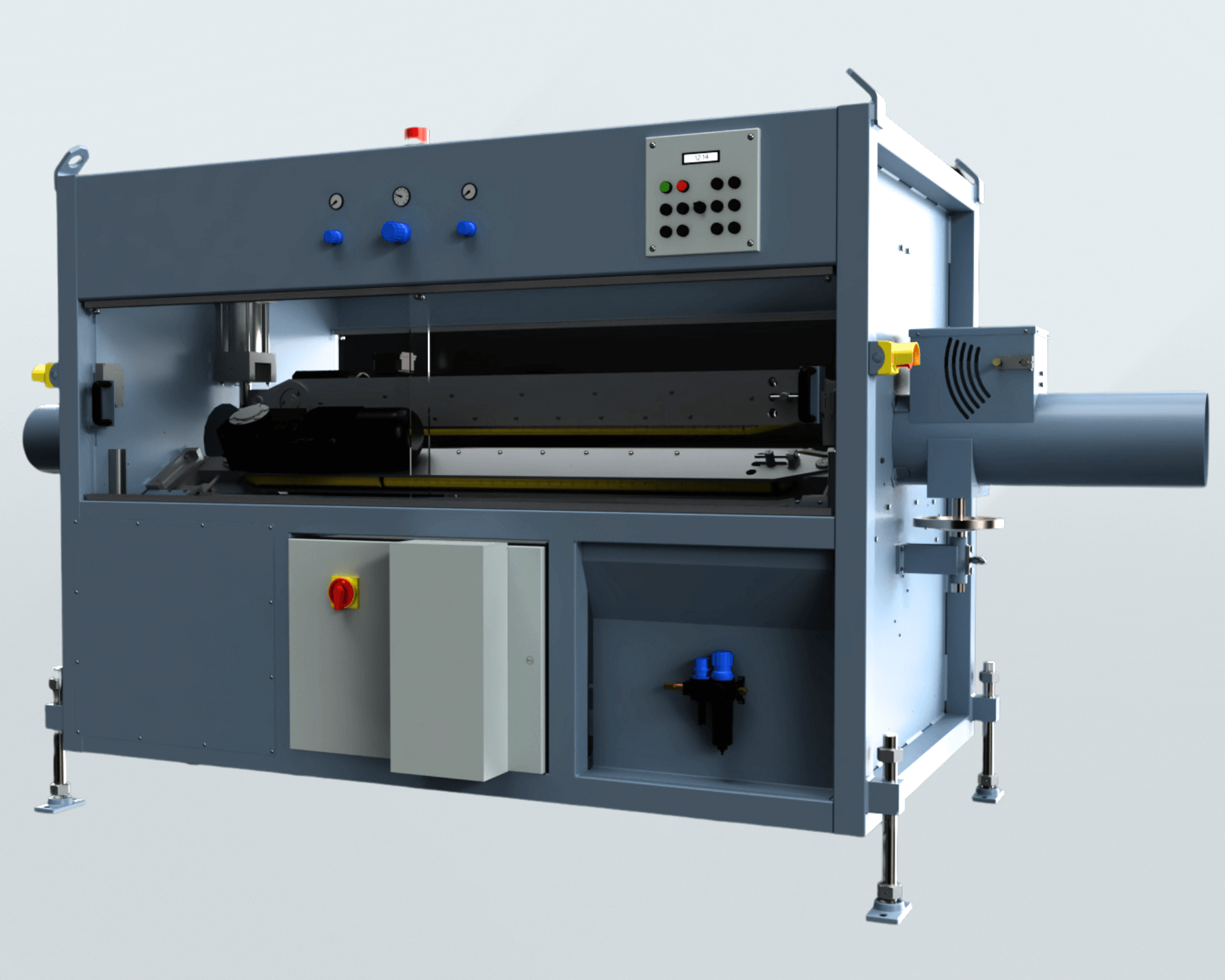
6. Cutting and Chamfering Machines
Cutting and chamfering machines are utilized to finish the pipe to its required length and prepare the ends for connection.
Rollepaal's pipe cutters are designed to change to a different pipe size quickly and easily without exchanging parts.
Read more about Pipe Cutters
.png)
By integrating these equipment, manufacturers can produce high-quality Multi-Layer pipes with consistent performance and cost-effectiveness. Each component plays a vital role in ensuring the overall efficiency and output of the production line.
Practical Implementation Considerations
The successful implementation of Multi-Layer extrusion requires careful consideration of several factors:
- Material Compatibility: The PVC chosen for each layer must be compatible regarding adhesion and processing characteristics to ensure a cohesive final product.
- Extrusion Equipment: Modern extruders, such as double screw extruders, provide the necessary precision and control for Multi-Layer processes. These machines have touch-screen controls that simplify operations and reduce training requirements.