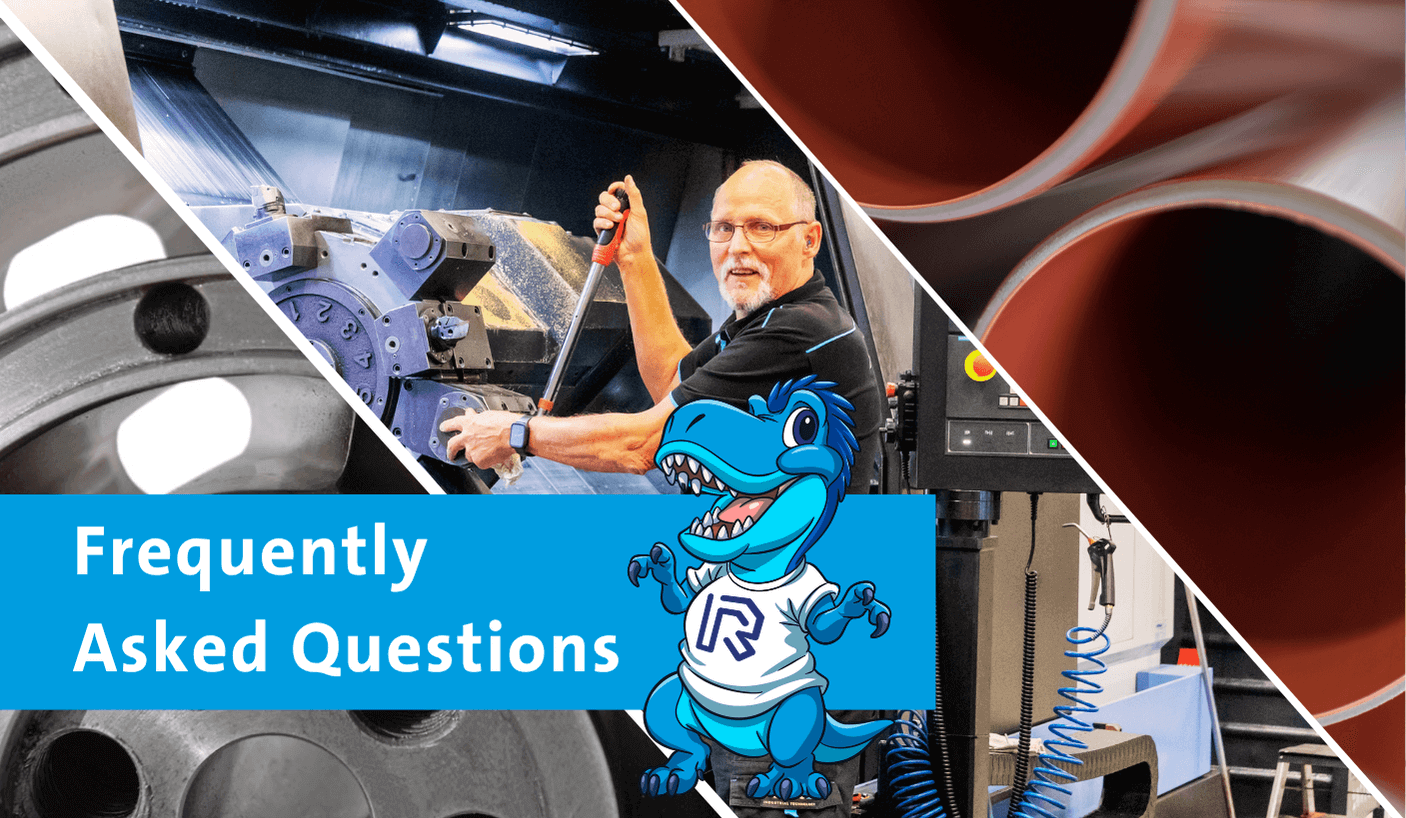
Here you’ll find clear and concise explanations of the most common and technical terms used in PVC pipe extrusion. Don’t see the term you’re looking for? Feel free to contact us!
A |
|
Additives |
Substances incorporated into PVC formulations to enhance properties such as stability, flexibility, and processability. Common additives include stabilizers, plasticizers, and lubricants. |
Annealing |
A heat treatment process applied to relieve internal stresses in extruded PVC pipes, improving dimensional stability and reducing the risk of cracking. |
Axial Orientation |
The alignment of polymer chains along the length of the pipe during the orientation process, enhancing tensile strength and impact resistance. |
B |
|
Barrel |
The cylindrical housing of the extruder that contains the screw and facilitates heating, melting, and conveying of PVC material. |
Biaxial Orientation |
A method where PVC pipe is stretched in both the axial and hoop directions, improving strength and impact resistance. Used in manufacturing PVC-O. |
C |
|
Calcium Carbonate (CaCO₃) |
A common filler in PVC formulations used to reduce material costs and increase stiffness. Excessive amounts can affect impact strength and processability. |
Calibration Sleeve |
A device used to shape and size the extruded pipe accurately, ensuring it meets specified dimensions during the cooling process. |
Conical Extruder |
A type of twin-screw extruder where the screws taper, traditionally offering more space for bearings but limiting processing optimization. |
Creep |
The gradual deformation of a pipe under constant stress over time, relevant for long-term buried pipe performance. |
D |
|
Die |
A metal tool at the end of the extruder that shapes the molten PVC into a pipe. |
Die Compression |
A design feature in extrusion dies that compresses the melt to ensure proper fusion and reduce visible weld lines (e.g. spider lines). |
Die Swell |
The expansion of PVC melt as it exits the die due to elastic recovery. |
Double Compression Die |
An advanced die design that compresses the melt twice, improving spider line weld quality, smoothness, and output range. |
Dry Blend |
A free-flowing powder mixture of PVC resin and additives, ready for extrusion, as opposed to pellets. |
E |
|
Extruder |
A machine that processes raw PVC by melting and forcing it through a die to create continuous pipe profiles. |
Extrusion |
The process of forming a continuous shape (such as a pipe) by pushing heated material through a die. |
F |
|
Feed Zone |
The section of the extruder where solid PVC material enters and begins heating. |
Filler |
Inert materials added to the PVC formulation to reduce cost and alter mechanical properties. Calcium carbonate is the most common. |
Fusion Level |
Degree of PVC gelation during processing, ideally 85–95%, measured using DSC or DCMT tests. Crucial for achieving mechanical strength. |
G |
|
Gelation |
The process where PVC particles fuse under heat and shear to form a uniform melt with tie molecules. |
Gravimetric Feeder |
A dosing system that measures and feeds material by weight for high precision. |
Grooved Feed |
A type of extruder barrel section with axial grooves that improve feeding consistency and output, especially with single-screw extruders. |
H |
|
Haul-Off Unit |
Equipment that pulls the extruded pipe through calibration and cooling zones at a regulated speed. |
Hoop Orientation |
The alignment of polymer chains circumferentially in the pipe wall, significantly increasing pressure resistance. |
I |
|
Impact Modifier |
Additives used to increase toughness and ductility in PVC, commonly applied in MPVC grades. |
In-line Measurement |
Continuous measurement of pipe diameter, wall thickness, or ovality during production to ensure dimensional accuracy. |
J |
|
Jet Cooling |
A method of rapidly cooling the pipe surface using high-velocity water or air jets to stabilize shape and dimensions. |
K |
|
K-Value |
A measure of the molecular weight of PVC resin. Higher values generally mean higher viscosity and strength. |
L |
|
L/D Ratio |
Length-to-diameter ratio of the screw in an extruder, influencing mixing efficiency, output, and residence time. |
Lubricant |
Additives that reduce friction during extrusion, ensuring smooth melt flow and preventing sticking or degradation. |
M |
|
Melt Strength |
The resistance of molten PVC to deformation. Critical for maintaining pipe geometry during processing. |
Minimum Required Strength (MRS) |
The extrapolated 50-year hydrostatic strength of the pipe material under constant pressure. |
Modified PVC (MPVC) |
PVC with added impact modifiers to improve ductility and point load resistance. |
N |
|
Notch Sensitivity |
The tendency of materials like PVC to initiate cracks at sharp notches or flaws. |
O |
|
Orientation |
The process of aligning molecular chains in a specific direction (axial or hoop) to enhance mechanical strength. |
Overjacketing |
A co-extrusion method where an outer layer is applied over a core pipe, often for UV resistance or impact protection. |
P |
|
Plasticizer |
Additives that increase flexibility of PVC—used in flexible products, not in rigid pipe applications. |
Poisson Effect |
The phenomenon where pipe length contracts under internal pressure due to lateral expansion. Relevant for joint design. |
Puller |
A mechanical unit that pulls extruded pipe through sizing, cooling, and cutting sections. |
PVC-O |
Oriented PVC, a high-strength pipe produced by biaxially stretching standard PVC, offering higher pressure performance with thinner walls. |
Q |
|
Quick Tool Change (QTC) |
A design feature enabling faster die and tooling swaps to reduce downtime and improve efficiency. |
Quenching |
Rapid cooling of the pipe after extrusion to set dimensions and physical properties. |
R |
|
Regrind |
Scrap PVC from the same production process that is ground and reprocessed into the extrusion line. |
Relaxation |
Reduction of internal stress over time in plastic pipes under constant deformation. Important for long-term performance. |
S |
|
Screw |
The rotating component within the extruder that melts and conveys PVC material along the barrel. |
SDR (Standard Dimension Ratio) |
The ratio of a pipe’s outer diameter to its wall thickness. Influences pressure rating. |
Spider Die |
A type of extrusion die for pipes that uses “spider legs” to hold the mandrel. Requires specific design to ensure proper fusion at weld lines. |
STIS (Specific Tangential Initial Stiffness) |
A measurement of pipe wall stiffness, used especially in non-pressure buried pipe standards. |
Structured Wall Pipe |
Pipes with specially designed wall profiles—such as foam core or corrugated—optimized for high stiffness with reduced weight. |
T |
|
Tie Molecules |
Polymer chains that span multiple crystalline regions, improving toughness and long-term strength. |
Torque Rheometer |
A lab instrument used to characterize PVC’s flow behavior under simulated processing conditions. |
Twin-Screw Extruder |
An extruder with two intermeshing screws, widely used in PVC processing due to superior mixing and melt quality. |
U |
|
uPVC (Unplasticized PVC) |
Rigid PVC used for pressure and non-pressure pipe applications due to its high strength and resistance. |
V |
|
Vacuum Venting |
A method of removing air and volatiles from the melt during extrusion, preventing voids and improving welds. |
Vicat Softening Temperature |
The temperature at which PVC begins to deform under a standard load. Indicates thermal performance. |
Viscoelasticity |
PVC melt behavior that exhibits both viscous flow and elastic recovery, important for fusion and die swell control. |
W |
|
Wall Slip |
Reduced friction between melt and barrel/die wall. Influences pressure, shear, and overall melt stability. |
Water Bath |
A cooling tank that stabilizes the extruded pipe by rapid temperature reduction. |
Weld Line |
A visible or structural interface in the pipe where two flow fronts meet—e.g. behind spider legs. Needs good design to avoid weak spots. |
Y |
|
Yield Strength |
The stress level at which PVC begins to plastically deform. Important for pressure pipe performance and calculations. |
Z |
|
Zone Heating |
Heating of extruder barrels in segmented zones to precisely control temperature at different stages of melting and mixing. |