3 min read
Comprehensive Comparison: PVC-O Batch Process vs. Inline Process
Albert Vaartjes
Jun 20, 2024 9:03:44 AM
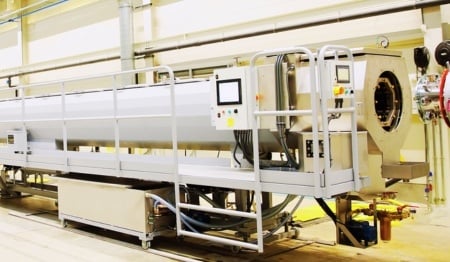
Industry professionals operating in the arena of PVC-O pipe production have two primary approaches they can employ - the Off-line (Batch) Process and the Inline (Continuous) Process.
PVC-O Batch versus Continuous - What's the Difference?
An Overview of the PVC-O Off-line (Batch) Process
The Batch Process begins with the manufacturing of a preformed pipe (feedstock pipe) characterized by an excellent wall thickness distribution and impeccable welding line quality. This preformed pipe is then cut into specific lengths, typically around six and a half meters.
The prepared pipe segments are subjected to a uniform heating process until they reach the stretching temperature. This heated pipe then gets inserted into a mold, following which the pipe ends are clamped. Subsequently, the pipe is expanded within the mold by applying internal pressure. It is then cooled while the internal pressure is maintained, and finally, the expanded pipe is taken out of the mold. The remaining unexpanded pipe ends are cut off.
An Inside Look at the PVC-O Inline (Continuous) Process
The Inline Process mirrors the Batch Process during the preliminary stage - the creation of the feedstock pipe with impressive wall thickness distribution and top-of-the-line welding line quality.
However, instead of cutting the pipe, the pipe is cooled and conditioned to the stretching temperature. This is followed by the direct expansion of the pipe on a mandrel as part of the continuous process. The pipe is then cooled and cut to any desired length without material wastage. Pipe dimensions are continuously optimized and controlled. If desired, a socket can be formed to the pipe using an inline socketing machine.
PVC-O Batch vs Continuous - Pros and Cons
When comparing the Batch and Continuous Processes, each showcases a distinct set of advantages and disadvantages.
Batch Process Advantages:
- The ability to include belling in the mold enables the creation of sockets without needing an additional Belling machine.
- Theoretical absence of diameter limits; pipes can already be produced up to 1200mm.
Batch Process Disadvantages:
- A requirement to machine and scrap for each pipe.
- A relatively high overweight due to unequal stretching.
- A fixed pipe length (usually 6 meters / 20 feet).
- The absence of integral quality control implies dealing with the produced pipe without an option for corrections during production.
- Increased energy consumption due to the pipe being heated and cooled twice during the creation of the feedstock pipe and final production of the pipe.
- Lower output for small pipe diameters due to the batch process's cycle time.
- The possible insufficient surface quality of the sealing area in the integrated socket is due to the outside calibration (mold) in combination with the wall thickness variations around the pipe.
Continuous Process Advantages:
- Lower overweight through inline wall thickness control and the presence of parameters for adjustment and optimization. Because we can start the line and then optimize dimensions and wall thickness, in practice this means that where batch processing shows an overweight of 8–18%, our continuous process runs overweight by only 3–5%.
- High-quality smooth pipe bore due to stretching on the mandrel. Something that avoids biofilms and reduces hydraulic resistance.
- The possibilities for variable pipe lengths, which save the cost of joints.
- Flexibility in socket and seal design
- High-quality sockets that are calibrated on the internal diameter. Practice has learned that the quality of the integral socket in sustained pressure testing is optimal at 15-20% additional length stretch, but the quality of the pipe remains similar.
- Relatively high production speed, especially for smaller diameters.
- Continuous control and data storage of all process parameters offer an early warning system for preventing rejects and full traceability of process conditions.
Please also consider these additional points while comparing the two processes:
- For the Batch Process, the cost of a preform extrusion line must be considered as an added investment.
- The space requirement in square meters is similar for both Batch and Inline Processes.
- An Rollepaal PVC-O extrusion line is shorter than a PE100 line with the same pressure class and output in meters per hour.
Concluding Remarks on PVC-O Batch and Inline Production Processes
In conclusion, the Batch and Inline Processes for producing PVC-O pipes each offer unique benefits and possess inherent limitations.
The Batch Process holds potential in terms of its flexibility in diameter application and its integral socket formation capabilities. However, it is marred by high energy consumption, lack of integral quality control, and low output for smaller-sized pipes.
Conversely, the Inline Process excels in terms of limiting material overweight, offering variable pipe lengths, higher production speeds for smaller diameters, and providing continuous quality control. Though, it doesn't offer the diameter flexibility observed in the Batch Process.
Each production method serves specific scenarios better than the other. Therefore, manufacturers need to make an informed choice based on their unique business models, customer requirements, and production capacities. Additionally, available resources and utility costs further sway this decision.
Explore the Innovative World of PVC-O: Production Processes, Technological Evolution, and Performance
Understand the PVC-O production techniques, technological advancements, and the superior performance attributes that set PVC-O apart in the industry. From the birth of bi-oriented pipes to the evolution of inline processes, and the innovative Rollepaal PVC-O production - our guide provides an informed and in-depth look into this remarkable material.