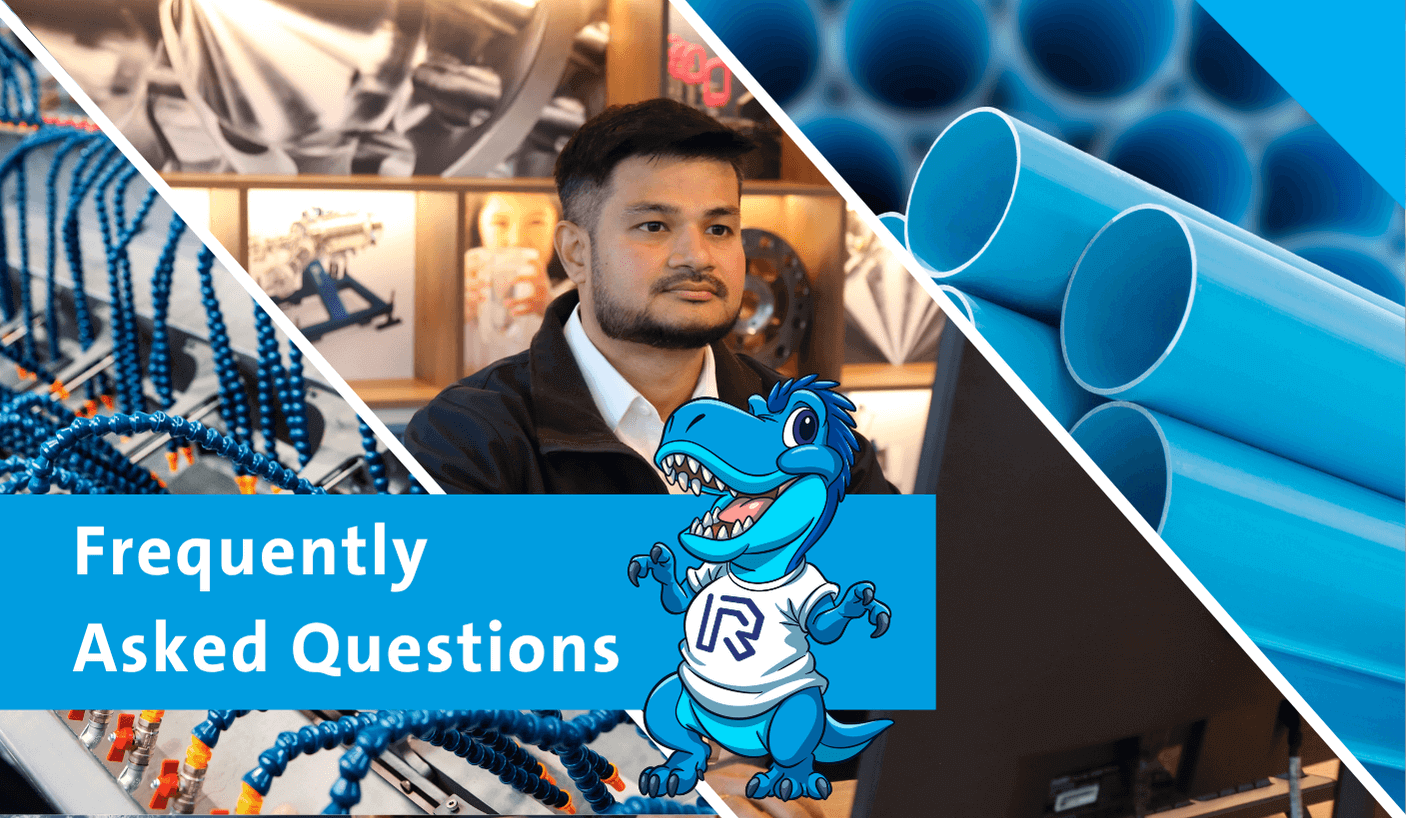
Plastic pipes offer distinct advantages over traditional materials due to properties like weight, corrosion resistance, flexibility, and ease of connection. This chapter primarily focuses on the extrusion process of pipes from high-volume commodity polymers: UPVC (Un-plasticised Poly Vinyl Chloride) and Polyolefins (PO), specifically HDPE and PP. These are further referred to as PVC, PE, and PP.
Processing Differences
The core difference in processing lies in the extruder type used and the material form. PVC extrusions are typically processed in dry blend form using a double screw extruder. In contrast, PO resin pipe grades are processed in granular form on single screw extruders.
Double screw extruders are well-suited for PVC extrusion because the material exhibits more wall slip than PO. Single screw extruders are commonly used for polyolefin pipe extrusion because it needs substantial heat input (approximately 3 times more than PVC) and isn't as prone to degradation.
The extrusion machine process differs accordingly: intermeshing double screws transport material via cavities independent of barrel friction, offering a higher pump efficiency. Dry blend is optimally processed on double screw extruders; using it on single screw extruders with a smooth intake is too dependent on friction for consistent output. Granulated PVC extrusion can be done on grooved single screws, but double screws avoid the granulation step and are self-wiping, leading to cost advantages.
PO pipe extrusion involves processing a real melt that crystallizes upon cooling. PVC, under extrusion conditions, behaves more like a rubber-like solid, forming a structure of tie molecules and crystallites in the pipe wall.
Modern high-grade plastic extrusion technologies for PO, using pipe extrusion machines, now share similarities with PVC pipe extrusion processes. They rely on forced transport, grooved intake, and short residence time at low shear in the die head to form an optimal structure.
This type of extrusion system and its benefits are also seen in extruded PVC tubing for specialized applications, where material consistency and dimensional stability are key.
T-Rex Extruder
Our T-Rex extruder is a perfect example of modern extrusion technology used in both PVC and PO extrusion systems. It reflects ongoing innovation in plastic extrusion process design.
Material Property Differences
Material properties differ significantly between PVC and PO. Generally, PVC is 2–3 times stronger and stiffer than PO, though its impact resistance is lower. Creep is higher for PO, which is relevant for buried pipe applications.
Diffusion through the pipe wall is lower for PVC, which is important for drinking water pipe extrusion in contaminated soil (brown fields). PVC pipe also has less risk of biofilm and is not vulnerable to chlorinated water, unlike PE pipe. PO materials allow oxygen diffusion, requiring barrier layers for hot/cold water applications.
In both materials, control over the extrusion machine and the overall plastic equipment setup plays a vital role in achieving optimal pipe performance.
Technical Specifications
Property |
PVC (UPVC) |
PO (PE/PP) |
Material Form (typical) |
Dry Blend |
Granular Form |
Extruder Type (typical) |
Double Screw |
Single Screw |
Relative Strength/Stiff |
Higher (2-3x) |
Lower |
Relative Impact Resist |
Lower |
Higher |
Relative Creep |
Lower |
Higher |
Relative Diffusion |
Lower |
Higher |
Chlorinated Water Vulner |
No |
Yes (PE) |
Bio-film Risk |
Less |
Higher |
Specific Energy (Drive) |
Lower |
Higher (approx. 3x) |
Volume Shrinkage (approx) |
0.7% |
3% |
FAQ Section
Why are different extruder types used for PVC and PO pipe production?
Due to differences in material form and behavior during processing, PVC extruder machines typically use double screw extruders, while PO uses single screw types to match their thermal and mechanical profiles.
How do the finished pipe properties differ between PVC and PO, affecting applications?
Differences in creep, diffusion, and mechanical strength define suitability. For example, plastic pipe extrusion for drinking water or high-pressure applications often favors PVC due to its lower permeability and higher rigidity.