2 min read
Energy Saving with Lower Extrusion Temperatures
Navdeep Singh Chawla
Jun 10, 2025 12:36:46 PM
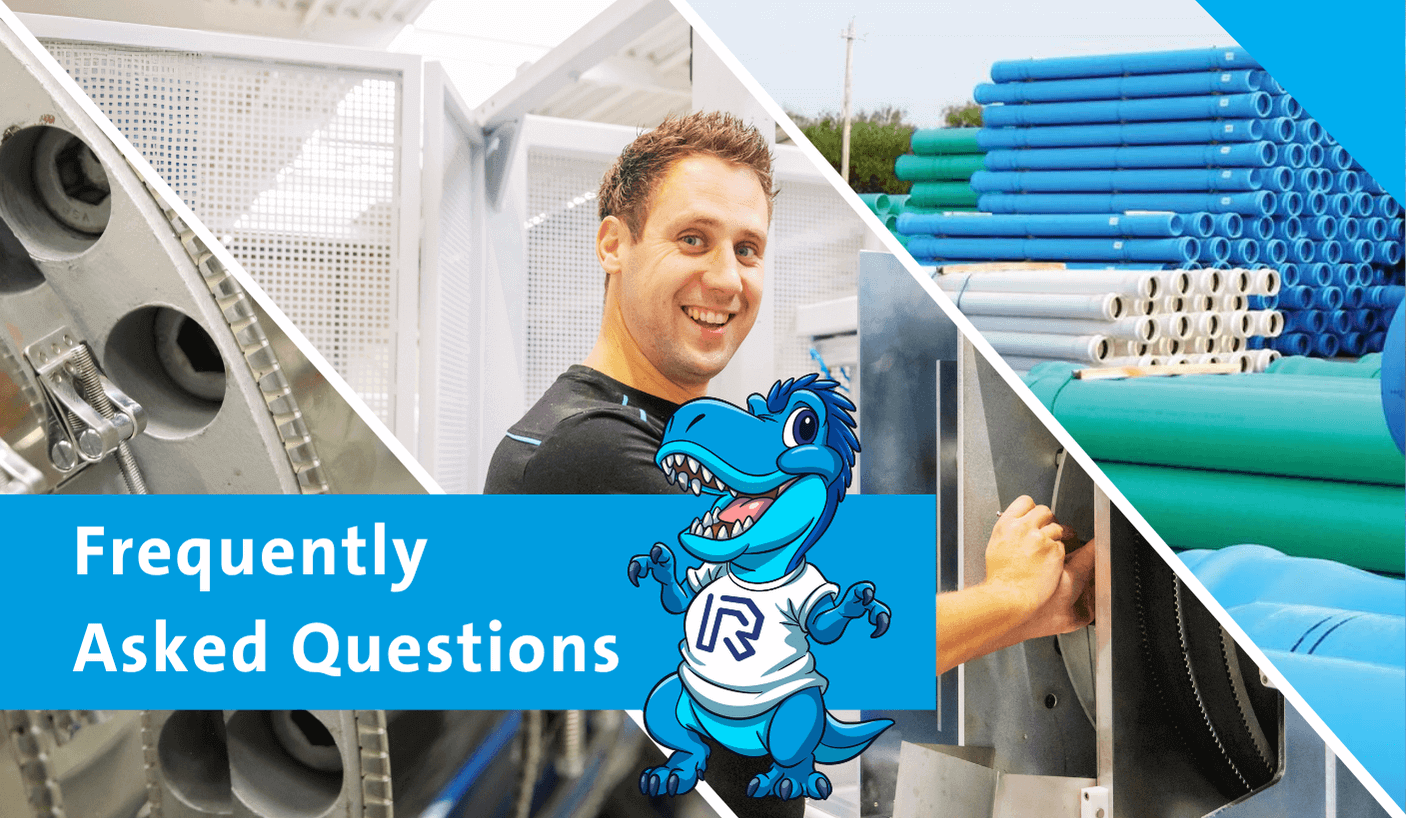
Optimizing Extrusion for Reduced Energy Consumption
Energy efficiency is a key aspect of reducing production costs and enhancing sustainability in plastic pipe extrusion. Modern extrusion pipe machine technology and optimized processing can significantly reduce energy requirements, especially specific energy (Wh/kg), across any pipe extrusion line.
Impact of Temperature and Cooling
The pipe extrusion process is energy-intensive, involving heating and mechanical work (drive energy). For PVC pipe extrusion machine operations, the material requires less heat input (approximately three times less specific energy in drive energy) than PO.
The design of the twin screw extruder and screws plays a critical role in energy use. For PVC extrusion machine configurations using twin screws, relying less on heavy cooling and more on energy from the motor (shear) to heat the dry blend effectively leads to lower specific energy consumption. A well-balanced screw design that avoids excessive cooling contributes to a "maintenance free" concept and higher reliability, further reducing costs from unexpected stops. Air cooling for the cylinder and closed internal screw cooling are preferred solutions that can reduce maintenance and energy usage compared to fluid-based systems.
Modern plastic pipe extrusion machine systems require approximately 100 Wh/kg (excluding the die) for a well-gelled PVC melt suitable for pressure pipes, compared to a theoretical minimum of around 80 Wh/kg. The die itself adds 15–25 Wh/kg, depending on its design and resistance.
Benefits of Lower Specific Energy
Lower specific energy consumption in any pipe extrusion machine directly translates to energy cost savings. Moreover, it enables higher output from the same extruder size. By reducing the energy that previously had to be removed via heavy cooling, more energy can now be used to prepare melt material, potentially increasing torque capacity and overall throughput on the extrusion pipe machine.
Technologically advanced plastic extrusion process designs eliminate the need for high pressures and inefficient cooling (energy loss). Well-engineered equipment with a wide processing window, supported by modern control systems (e.g., Windows-based interfaces), enables reproducible, energy-efficient pipe extrusion operations.
Technical Specifications/Considerations:
-
Specific Energy (PVC): Approx. 100 Wh/kg (extruder), 15–25 Wh/kg (die). Theoretical minimum: 80 Wh/kg.
-
Specific Energy (PO): Approx. 3x higher drive energy than PVC.
-
Cooling Method: Air cooling and closed internal screw cooling preferred over fluid systems.
-
Extruder Design: Balanced twin screw extruder design reducing reliance on heavy cooling systems.
FAQ Section
How does extruder design impact energy consumption?
Extruder and screw design can significantly impact energy use. Designs that efficiently transfer motor energy (shear) to the material and require less heavy cooling (e.g., air cooling, closed internal screw cooling) lead to lower specific energy consumption.
What are the benefits of achieving lower specific energy in extrusion?
Lower specific energy directly reduces energy costs per pipe length. It also potentially allows for higher output from the same extruder size by utilizing energy previously removed by cooling to process more material.