3 min read
Multi-Layer Die-Head Technologies for PVC Pipe Extrusion
Michan Katerbarg Feb 10, 2025 1:55:21 PM
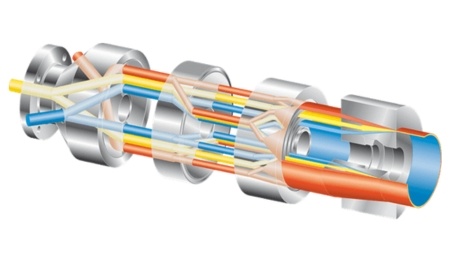
Precise distribution flow is crucial in the production of high-quality multi-layer PVC pipes to ensure uniform wall thickness, material efficiency, and structural integrity. Die-heads play a vital role in achieving these objectives, and the choice of technology—coathanger or branching—directly impacts the production process.
Since Rollepaal is the only company in the world producing die-heads with patented branching technology, we will explain the differences between these technologies and their suitability for PVC pipe production. We will start with the technology used by all of our competitors, the so-called coat hanger technology.
Coathanger Technology
Design
Coathanger die-heads get their name from their shape, which resembles an inverted coathanger. The molten PVC material enters the die-head through a central inlet and spreads through a tapered manifold. This manifold is designed to balance the pressure and velocity of the material as it moves towards the die's exit.
In this image, you can see that the material flows from one point into the die-head.
Flow Management
The tapered manifold helps distribute the material across the die's width. While effective for flat, planar geometries, the flow dynamics of coathanger technology are less suitable for circular shapes, such as pipes. Uneven flow patterns often lead to areas of varying thickness. As illustrated in this image, this uneven flow pattern impacts the shape of a plastic pipe and causes an overweight of the pipe of 3 to 5%.
Limitations for PVC Pipes
Uneven Wall Thickness: In circular dies, the coathanger design struggles to maintain uniform flow distribution. This results in pipes with inconsistent wall thickness, leading to thicker sections that compromise material efficiency and product quality. The image shows a plastic pipe with weld line, due to uneven wall thickness.
- Material Waste: Overweight pipes are a common issue, as excessive thickness in some areas increases material usage unnecessarily. A pipe extrusion line with a coathanger die head would produce a 3 to 5% overweight pipe.
- Application Misalignment: Coathanger technology is optimized for flat products like films and sheets but is inherently unsuited for the radial symmetry required in pipe extrusion.
Applications
- Best suited for flat products such as sheets, films, and coatings.
- Inefficient for circular products like PVC pipes.
Rollepaal Branching Technology
Design
Rollepaal Branching die-heads use a unique patented design where the molten material flows through multiple channels or branches, which are carefully engineered to ensure equal distribution of material. These branches merge into a standard cavity or manifold, directing the material uniformly towards the die's exit, resulting in a pipe with a perfect distribution in the circumference.
Flow Management
The branching design is tailored explicitly for circular geometries. It ensures even flow distribution around the circumference of the die, resulting in uniform wall thickness and eliminating variations that could compromise the pipe's structural integrity.
Advantages for PVC Pipes
- Best-in-Class Wall Thickness: Rollepaal Branching Technology excels at maintaining best-in-class wall thickness distribution across the entire circumference of the pipe, which is critical for multi-layer pipes.
- Material Efficiency: The precise flow control minimizes material wastage by preventing areas of excessive thickness, producing lightweight, economical pipes.
- Multi-Layer Capability: Rollepaal Branching Technology ensures even flow distribution for each layer, maintaining the top-notch skin-core ratios and overall layer consistency in multi-layer pipe production.
- Optimized for PVC: The branching design handles PVC's viscosity variations very well, ensuring smooth and uniform flow.
Applications
- Ideal for producing circular products like PVC pipes.
- Effective for multi-layer pipes, meeting stringent quality and material efficiency requirements.
Comparative Overview
Aspect |
Coathanger Technology |
Branching Technology |
Design Complexity |
More complex for circular geometries |
Moderate and optimized for pipes |
Flow Uniformity |
Inconsistent for circular shapes |
Consistently high |
Material Efficiency |
Low, due to overweight sections |
High, due to even distribution |
Applications |
Films, sheets, and flat products |
Multi-layer and Solid Wall PVC pipes |
Suitability for Pipes |
Suboptimal |
Superior |
Conclusion
Rollepaal Branching Technology is the clear choice for producing multi-layer PVC pipes. It provides even flow distribution, ensures uniform wall thickness, and minimizes material waste. While effective for flat products, coathanger technology is inherently unsuitable for circular geometries and would lead to inefficient, overweight pipes.
By leveraging Rollepaal Branching Technology, manufacturers can achieve high-quality, economical PVC pipes that meet the demands of modern production standards without an overweight of 3 to 5% in circumference distribution, compared to the coathanger technology. Every pipe producer can calculate what it means to save 5% of material costs on the total production of PVC pipes. In practice, you can earn your die-head back within a year. The good thing is that our die-heads are in the same price range as most in the market.
In addition, our branching technology allows you to install a new die-head capable of producing multi-layer and solid wall pipes. With the same die head, you can produce both types of pipes.
We have over 30 years of experience with this technology and have installed over 400 multi-layer die-heads worldwide. Are you interested in replacing your old die-heads and making the most economical choice for your factory? Contact us, and we will help you optimize your production process.